HSK Tool Holders, like other tool holders, are devices that are used in metal and wood milling. The majority of Tool Holders have a conical design of the taper (Morse taper), which is called the male part, that fits the internal (female) receiver design of the machine’s spindle. The spindle is the part of the machine that is connected to the gearbox and is rotated at different speeds. The part of the tool holder that is projected from the spindle is where the tools are fixed. Tool holders come in different sizes and standards with variations of the shank and the flange.
About HSK Tool Holders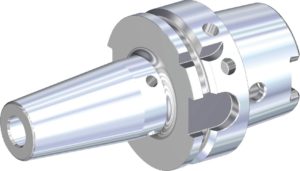
Despite its growing use and acceptance in the United States, HSK technology remains widely misunderstood. Questions about its proper use have created substantial resistance among those who are accustomed to traditional, steep-taper shanks, including CAT, SK, and BT. Although a significant portion of the machine tools imported to the United States from Europe incorporates HSK spindles, steep-taper shanks still represent the most widely used tooling interface. The acronym “HSK” is the German abbreviation for “hollow taper shank.”
One of the top-used tool holder standards is HSK; it is a relatively new design. These tools do not have the retention knob (pull stud), and their unique feature is the hollow shank. This design was created with high-speed machining (HSM) in mind. Therefore, these tool holders have to be balanced with high precision, and it is strongly recommended to use specific balancing equipment if you are working with operations that require exceptionally high rotation speeds.
HSK tool holders require a much higher level of manufacturing compared to other types of tool holders because the tolerance between the spindle receiver and the taper is less than two microns (.002 mm). They are extremely delicate devices and should be stored in a safe place where no misbalancing damage can occur.
HSK tool holders support the technology of ATC (Automated Tool Change) and are a reliable choice for high-speed machinery, both in terms of rotation speed and speed of manufacturing. They are lighter and balanced with the highest precision, thereby making them a top choice of professional CNC machine operators all over the world.
HSK Tool Holders 101
HSK shanks address three different application categories:
- Types A and C serve applications requiring moderate torque and moderate-to-high spindle speeds. (Type A is for automatic tool changing, and Type C is for manual changing.)
- Types B and D are designed for high torque applications with moderate-to-high spindle speeds. (Type B is for automatic changing, and Type D is for manual changing.)
- Types E and F are designed for low torque and very high spindle speeds on machines that incorporate ATCs.
Comparing HSK With Steep Taper
Although HSK has become the primary choice for newly developed machine tools in Europe, substantial skepticism remains in the United States. To alleviate some of this doubt, it’s important to explain some fundamental differences between HSK and conventional tooling interfaces.
The first category of comparison is radial and axial stiffness – the most important aspects of any machining operation. Unlike conventional shanks, an HSK shank is hollow and the clamping mechanism operates from the inside.
HSK holders incorporate two drive slots that engage drive keys in the spindle receiver. When clamped into the receiver, the wall of the hollow shank deflects slightly. Radial access holes in the shank’s wall allow the clamping mechanism to contact an actuation screw. The inner surface of the shank wall also incorporates a chamfer to facilitate clamping.
Although different clamping methods are available (depending on the tooling manufacturer), all HSK receivers incorporate segmented collets that expand radially under drawbar pressure to bear against the inner wall of the shank.
Because the collet’s chamfer matches the chamfer of the shank’s inner wall, the shank is locked securely into the receiver when the drawbar is actuated. When this occurs, elastic deformation of the shank’s walls creates firm metal-to-metal contact around the shank, as well as mating the shank’s flange with the receiver. (See Figure 3, above.)
Assuming that equivalent force is applied to the drawbar, twice as much clamping force is exerted on the flange of an HSK shank compared to a steep-taper shank. This extra clamping force makes the radial stiffness of HSK tool holders up to five times greater than the value for CAT, SK, or BT.
HSK Shank (Hollow Taper Shank System)
HSK shank standard is also known as ISO 12164, DIN 69893, DIN 29893-1, and DIN 69063-1.
The taper on all HSK shanks is 10:1.
The flange groove on forms A, B, E, and F is 60 degrees
HSK-A DIN 69893-1:1996-01
Size |
Form |
D–1 |
D–2 |
L–1 |
L–2 |
L–3 |
B–1 |
B–2 |
B–3 |
H–1 |
H–2 |
63 |
A |
48 |
63 |
58 |
26 |
10 |
12.5 |
16 |
18 |
26.5 |
20 |
Bottom Line
The HSK interface also offers some key advantages in relation to high-speed machine spindles, tool collisions, and maintenance. When using a conventional interface (CAT, SK, BT) at spindle speeds greater than 8,000 rpm, the spindle receiver expands at a much higher rate than the tool holder shank. With its hollow design, however, the HSK shank acts as a fuse during collisions. When a cutting tool crashes, the tool holder breaks off and protects the spindle, thus reducing repair costs and machine downtime.
Shop Superior Machine & Tool’s selection of HSK Tool Holders