Understanding Absolute Mode (G90) Vs Incremental Motion: CNC Machines
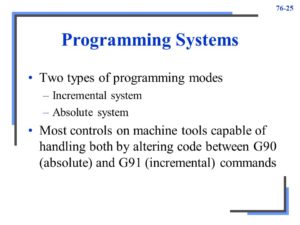
Incremental system. Absolute system. Most controls on machine tools capable of handling both by altering code between G90 (absolute) and G91 (incremental) commands.
All considerations to this point accept that the absolute mode of programming is used. The CNC word used to refer to the absolute mode is G90.
In absolute mode, the end points intended for all motions will be identified from the program zero point. For beginners, this is typically the best and least complex method of identifying end points for motion commands. However, there are alternative methods of stating end points for axis motion.
Dont know about motion? Read our article here.
In incremental mode (generally stated by G91), end points for motion are identified from the tool’s present position, not from program zero. With this technique of imposing motion, the programmer must always be asking “How far must I transfer the device?”
While there are still periods when the incremental mode can be helpful, generally speaking this is the clumsier way of stating motion and learners should focus on using absolute mode.
Be cautious while building motion commands. Learners have the tendency to consider incrementally. If functioning in the absolute mode (as learners should), the programmer should constantly be questioning “To what circumstances must the device be moved?” This condition is comparative to program zero, NOT from the apparatus’s existing position.
Apart from making it very simple to decide the present point for one command, another advantage of functioning in absolute mode has to do with errors made over the course of motion commands.
In absolute mode, if a motion error is made in one command of the program, simply one movement will be inappropriate. On the contrary, if an error is made in the course of incremental movements, all motions from the point of the error will also be inappropriate.
Allocating Program Zero (Absolute Mode)
Remember that the CNC control must state the site of the program zero point by one means or another. How this is completed differs widely from one CNC machine and control to another. An (older) technique is to consign program zero in the program.
With this technique, the programmer tells the control how far it is from the program zero point to the preliminary point of the machine. This is usually completed with a G92 (or G50) command at least at the starting of the program and perhaps at the beginning of every device.
A different, fresher and improved way to allot program zero is to use some form of offset. Normally, machining midpoint control producers call offsets used to allocate program zero fixture offsets. Turning center manufacturers usually call offsets used to consign program zero for every tool geometry offsets. Further on how program zero can be allocated will be accessible through theory number four.
Ref: cncci.com